When PrecisionParts Manufacturing, a mid-sized producer of industrial machine components, decided to outsource its IT and technology support, it seemed like a cost-effective way to modernize its aging systems. The partnership with ApexTech Solutions, a well-regarded technology service provider, promised seamless operations, enhanced cybersecurity, and better data integration. Instead, the venture exposed significant cracks in both PrecisionParts’ operations and ApexTech’s capacity to manage a challenging customer.
The Manufacturer’s Challenges
PrecisionParts was typical of many manufacturing businesses: dependent on legacy systems that had served them well for decades but were woefully unprepared for modern digital demands. Inventory management relied on outdated spreadsheets, production lines operated with minimal automation, and cybersecurity was an afterthought.
When PrecisionParts experienced its first ransomware attack, it became painfully clear that something had to change. ApexTech was brought in to implement a cloud-based Enterprise Resource Planning (ERP) system, upgrade the production line’s IoT capabilities, and secure the company’s digital infrastructure.
What ApexTech encountered was a perfect storm:
- Outdated Systems: PrecisionParts’ patchwork IT infrastructure made integration difficult and time-consuming. Many machines were too old to support IoT upgrades, requiring costly retrofits.
- Resistance to Change: Employees were wary of the new technology, fearing job loss or a steep learning curve. This led to delays in adoption and training gaps.
- Undefined Expectations: PrecisionParts leadership failed to clearly articulate their goals or assign internal project managers, creating a communication breakdown with ApexTech.
The Contractor’s Struggles
ApexTech Solutions was no stranger to tough projects, but PrecisionParts pushed their limits. Several issues surfaced during the partnership:
- Scope Creep: What began as a straightforward ERP implementation ballooned into a full-scale overhaul of PrecisionParts’ operations, with no additional time or budget allocated.
- Underestimating Complexity: ApexTech’s initial proposal failed to account for the intricacies of integrating modern technology into a manufacturing environment reliant on analog systems.
- Customer Frustration: PrecisionParts grew impatient with delays and unanticipated costs, straining the relationship. Frequent leadership turnover at PrecisionParts further complicated decision-making.
ApexTech’s team worked overtime to keep the project on track, but mounting frustrations led to mistakes. During one critical system upgrade, ApexTech inadvertently triggered a production line shutdown that lasted 36 hours. The downtime cost PrecisionParts thousands of dollars in lost output, further souring the partnership.
A Cautionary But Common Tale
In today’s hyper-competitive global marketplace, manufacturers can’t afford to rely on yesterday’s technology. While many industries have embraced digital transformation, a surprising number of manufacturing businesses continue to operate with outdated systems and limited cybersecurity measures. This lack of technological maturity not only hinders productivity and growth—but also leaves companies vulnerable to cyberattacks, data breaches, and lost customer trust.
Why Manufacturing Must Embrace Digital Transformation
1. Increased Efficiency and Lower Costs:
Smart factories powered by automation, IoT devices, and advanced analytics help manufacturers streamline operations, reduce downtime, and optimize the use of raw materials. By upgrading legacy systems, businesses can unlock real-time insights that drive innovation and efficiency—ultimately improving the bottom line.
2. Enhanced Competitiveness in a Crowded Market:
Today’s customers expect high-quality products delivered at record speed, and they favor partners who can adapt quickly to shifting market demands. Companies leveraging Industry 4.0 technologies, such as AI-driven predictive maintenance and digital twins, can outpace competitors that are still stuck with manual processes and limited data visibility.
3. Strengthened Cybersecurity and Data Protection:
As supply chains become more interconnected, cybersecurity threats increase exponentially. Outdated software, lackluster firewalls, and limited threat detection tools leave manufacturers wide open to cyberattacks that can jeopardize intellectual property, proprietary trade secrets, and sensitive customer information. Investing in updated technology—secure cloud platforms, end-to-end encryption, and advanced intrusion detection systems—fortifies your organization against both current and emerging threats.
The High Stakes of Falling Behind
Reputation and Customer Trust:
A single data breach can severely damage your brand’s reputation. In an environment where customers demand data security and privacy, failing to modernize puts valuable relationships at risk. Losing trust can be far costlier than any single cybersecurity investment.
Regulatory Compliance and Legal Ramifications:
With stringent global regulations—from GDPR to CCPA—governing data protection, non-compliance could result in hefty fines and legal battles. By embracing updated technology and best-in-class cybersecurity practices, you ensure that compliance becomes a natural byproduct of your operations.
Talent Acquisition and Retention:
Modernizing your manufacturing tech stack not only appeals to partners and customers—it also attracts forward-thinking talent. Employees increasingly seek out companies that invest in the latest tools and provide ongoing training, enabling them to work smarter and advance their careers.
Practical Steps to Advance Your Tech Maturity
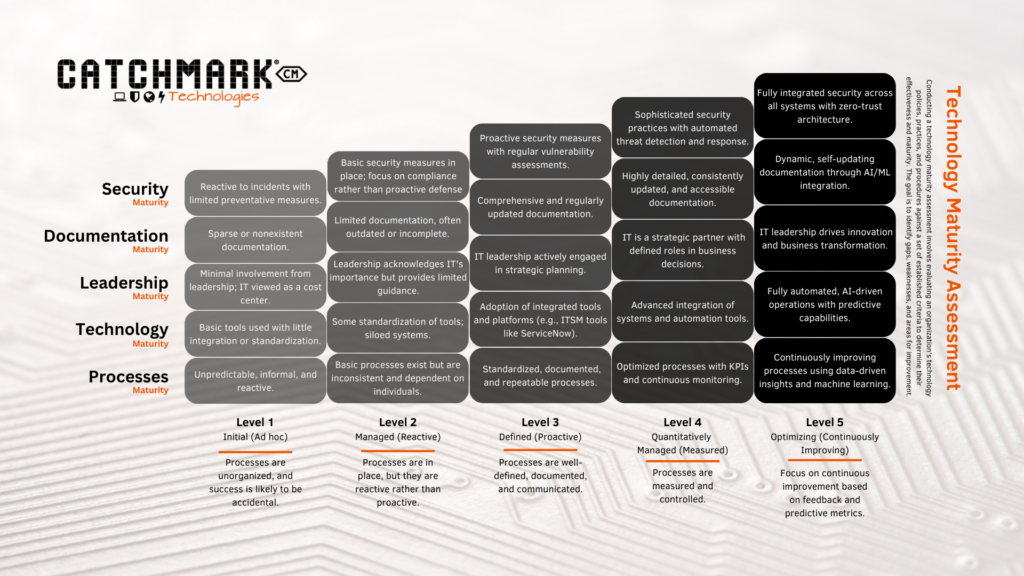
1. Assess Your Current Infrastructure:
Begin with a comprehensive audit of your existing systems. Identify outdated equipment, software vulnerabilities, and skills gaps. This assessment serves as a roadmap, guiding where to invest for maximum ROI.
2. Prioritize Cybersecurity from the Start:
Build cybersecurity into every layer of your digital ecosystem. Implement multi-factor authentication, regularly update security patches, and employ continuous monitoring tools that detect and neutralize threats before they cause damage.
3. Leverage the Cloud for Scalability and Security:
Cloud-based manufacturing solutions offer flexibility, on-demand storage, and built-in security features that surpass legacy on-premises systems. Plus, the cloud enables seamless integration with cutting-edge AI and machine learning platforms.
4. Invest in Workforce Development:
Training employees to understand digital tools and cybersecurity best practices is critical. Your workforce should know how to spot phishing scams, safeguard valuable data, and optimize production lines using the latest technologies.
Embrace the Future or Risk Irrelevance
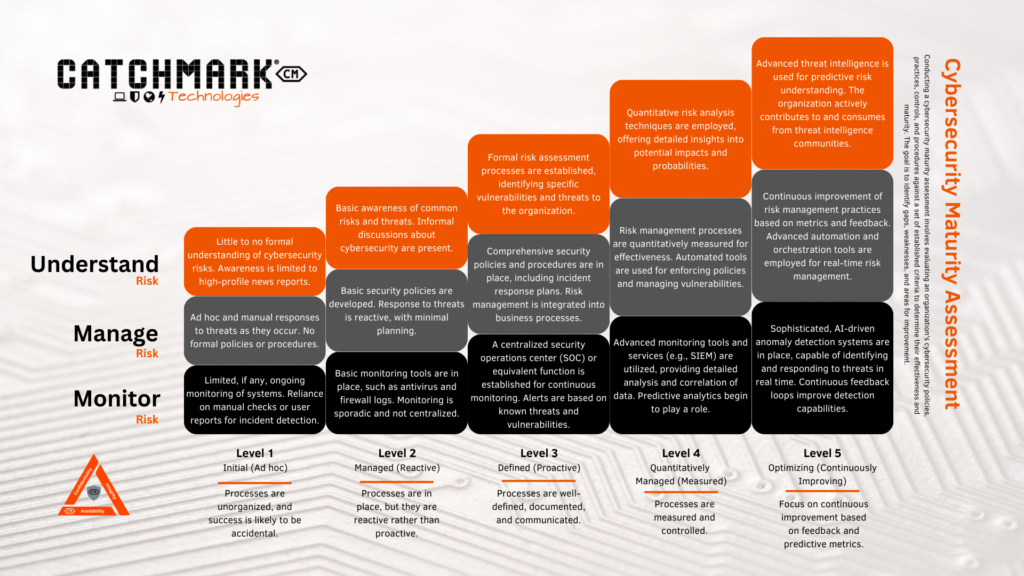
The message is clear: remaining tied to outdated systems and minimal cybersecurity measures is no longer viable. By investing in modernization, manufacturing businesses can boost operational efficiency, stay ahead of the competition, and safeguard their most valuable assets—customer data and intellectual property.
In an era defined by Industry 4.0, manufacturers that embrace digital transformation and robust cybersecurity protocols will thrive. Those that do not risk being left behind, facing eroded trust, lost opportunities, and potentially crippling data breaches. The time to invest is now, ensuring your organization’s continued success, security, and relevance in the manufacturing landscape of tomorrow.
Lessons Learned
For PrecisionParts, the experience was a wake-up call. Leadership realized the importance of aligning internal processes with technological upgrades and committed to appointing a dedicated project manager for future initiatives. They also invested in comprehensive employee training and established regular cybersecurity audits.
For ApexTech Solutions, the ordeal highlighted the need for stronger project vetting. They began requiring more detailed assessments before taking on clients with aging infrastructure and ensured contracts included clear definitions of scope, timelines, and shared responsibilities.
The Road to Recovery
Though the relationship between PrecisionParts and ApexTech was strained, both parties eventually found a way forward. By focusing on communication, managing expectations, and acknowledging shared accountability, they successfully completed the project. Today, PrecisionParts operates a more secure, efficient, and connected manufacturing facility.
The experience, while painful, was transformative for both organizations. It demonstrated the critical importance of collaboration, realistic planning, and the acknowledgment that true digital transformation requires not just the right tools—but the right mindset and commitment from everyone involved.
Need Help
At CatchMark Technologies, we understand the unique challenges manufacturers face in today’s fast-paced, technology-driven world. With expertise in IT support, cybersecurity, and digital transformation, we help manufacturers modernize their operations, protect critical assets, and achieve long-term success. Whether it’s implementing smart factory solutions, safeguarding sensitive data, or providing hands-on employee training, CatchMark delivers tailored solutions designed to meet the specific needs of your business. Don’t let outdated systems hold you back—partner with CatchMark Technologies to turn challenges into opportunities and ensure your business thrives in the modern manufacturing landscape. Contact us today to learn more!